Многие компании автоматизируют собственные бизнес-процессы, чтобы работать эффективнее. Но идеальный вариант – это когда результаты автоматизации не только повышают эффективность внутренних процессов, но и улучшают уровень клиентского обслуживания. Так бывает не всегда, но многим компаниям это удаётся. Например, предприятие «Архио» автоматизировало собственное производство, чтобы клиенты тратили меньше времени на монтаж его изделий. О том, какие внутренние процессы пришлось перестроить для достижения этой цели, порталу Biz360.ru рассказал Дмитрий Чумичев, директор компании «Архио».
Дмитрий Чумичев – директор и совладелец компании «Архио». Окончил МИРЭА по специальности «Информационные системы». Открывал несколько собственных бизнесов, в каждом из которых занимался автоматизацией процессов и выстраиванием информационных систем. Компания «Архио» была основана в 2002 году в Подмосковье, специализируется на производстве фасадного декора.
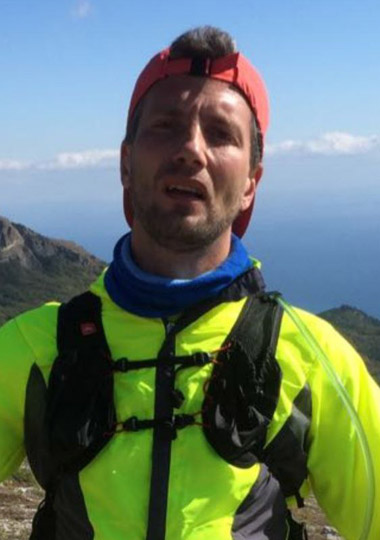
Наша компания «Архио» производит фасадный декор из полимербетона. Этот материал выглядит так же, как натуральный камень – например, известняк, песчаник или мрамор. Но при этом он гораздо легче, не такой хрупкий, не такой дорогой и не требует сложного монтажа. Благодаря нашему декору нагрузка на фасад здания не увеличивается. Мы предлагаем балюстрады, декоративные колонны, пилястры, русты и другие декоративные элементы, предназначенные для отделки фасадов и интерьеров.
Технологию производства фасадного декора из полимербетона мы запатентовали в 2005 году. А в 2006-м стали первой компанией в России, которая начала выпускать эту продукцию. Наше производство находится в подмосковном Дмитрове, а клиенты – по всей стране. Мы сотрудничаем как с конечными покупателями, так и с корпоративными заказчиками – застройщиками, архитектурными студиями, дилерами. Не производим продукцию «на склад», а работаем под заказ.
В 2019 году мы открыли новую производственную площадку и улучшили автоматизацию производственных процессов. У меня айтишное образование, я уже реализовал несколько проектов по автоматизации, поэтому понимал, что и как следует делать в собственной компании. Вместе с командой мы формулировали техзадание и то, как должны выглядеть процессы после внедрения информационной системы. В качестве подрядчика мы выбрали компанию «Айтон», которую порекомендовали знакомые предприниматели.
На первом этапе мы автоматизировали с помощью IT-решения «1С:Управление нашей фирмой» обработку заявок от клиентов и расчёт плана производства. Это потребовалось, чтобы оптимальным образом выстроить процесс производства. Нам хотелось по максимуму задействовать свои ресурсы – с одной стороны, с другой – чтобы клиенты вовремя получали нашу продукцию. После успешной реализации этого проекта мы перешли к следующему этапу автоматизации.
Дело в том, что наши клиенты оформляют фасад дома с использованием многочисленных декоративных элементов. Их завозят на объект, изделия уложены на палеты и замотаны стрейч-пленкой, а строителям нужно разобраться, какие детали и где находятся. После этого – понять, как их установить на фасаде. Задача не из лёгких! Например, большая арка может состоять более чем из 170 фрагментов, а изделия для неё уложены на 15 палет.
От монтажников мы услышали такое пожелание: им бы хотелось при поступлении декора на стройплощадку сразу понимать – где на фасаде и как именно эти детали должны размещаться. Ранее им приходилось перебирать всю продукцию в поисках нужного артикула, а затем по бумажным чертежам сверять, что и куда монтировать. Нередко изделия повреждались при перекладывании, а декор терял товарный вид. Наши конечные пользователи на самом деле – именно монтажники. От того, как они сработают, зависит, останется ли доволен наш клиент.
Мы решили пересмотреть принцип формирования палет: чтобы на каждую выкладывались элементы декора для одного комплекта – например, облицовки одного окна. Но для решения этой задачи нам требовалось пересмотреть свои внутренние процессы и связать этап проектирования, производства и комплектации в единую неразрывную цепочку. Также необходимо было построить последовательность производства изделий в соответствии с порядком монтажа декора на объекте.
Мы использовали уже внедрённое решение «1С:Управление нашей фирмой» (далее – «1С:УНФ»). Этот программный продукт является практически единственным решением на рынке, которое подходит производственным компаниям и не требует значительных финансовых вложений.
Каждое изделие после выпуска проходит проверку качества. Раньше наши сотрудники отдела технического контроля (ОТК) работали с готовой продукцией, не понимая, для какого заказа она выпущена. На участок ОТК поступают изделия для десятков заказов, находящихся в данный момент в производстве.
Сотрудник должен проверить параметры изделия, сверяясь с чертежом. Раньше на каждой выпущенной детали фломастером писали её артикул. Сотрудник видел его и искал в стопке бумажных чертежей тот, который соответствовал этому изделию. Мы можем выпускать одновременно продукцию по 500 артикулам. Представляете, каких размеров была стопка с чертежами к ним?
Иногда артикулы отличаются одной цифрой или буквой. Сотрудник тратил довольно много времени, чтобы найти нужный чертёж. Бывали ситуации, когда чертёж ещё не распечатали, и тогда приходилось идти в офис за нужным документом. Или контролёр ОТК начинал проверять изделие по неверному чертежу.
Мы создали автоматизированное рабочее место «Производство» в программе «1С:УНФ», чтобы выстроить этот процесс иначе. Теперь при запуске заказа в производство в учётную систему подгружаются чертежи всех изделий комплектов, которые будут из них собраны.
На каждое изделие наносится штрих-код с информацией об его артикуле. Сотрудник ОТК сканирует штрих-код. На его рабочем месте установлен большой монитор, на котором открывается чертёж. Сотрудник видит все размеры и сверяется с ними при проверке изделия. Ему не нужно искать бумажный чертёж. Теперь исключены ситуации, когда он по невнимательности работает с другим чертежом. Скорость проверки увеличилась в три раза.
Если изделие соответствует всем параметрам, сотрудник ОТК распечатывает из системы и приклеивает на него наклейку с QR-кодом и штрих-кодом.
Раньше мы комплектовали изделия вразнобой. Это происходило потому, что мы не учитывали при формировании палет то, как из выгруженной на них продукции собираются комплекты. Комплектовщик брал изделие, видел его артикул, написанный вручную, и, сверяясь с документами, понимал, для какого заказа оно произведено. Затем находил палеты по заказу и на них складывал продукцию так, как ему было удобнее.
Мы создали автоматизированное рабочее место «Комплектация», чтобы все элементы декора для каждого комплекта укладывались на одну палету. Наши сотрудники с помощью терминалов сбора данных считывают с каждого изделия штрих-код с его серийным номером. Терминал подсказывает, на какую палету следует положить декор. У каждой палеты тоже есть свой штрих-код. Прежде, чем положить на неё изделие, сотрудник участка комплектации считывает штрих-код палеты. Это делается для того, чтобы не перепутать палеты. Если сотрудник хочет положить продукцию не туда, терминал сбора данных предупредит его об ошибке.
- Михаил Пинягин, директор компании «Айтон»: «Автоматизированные рабочие места (АРМ) довольно популярны и используются во многих компаниях. Основной задачей при их разработке является учёт всех возможных сценариев, через которые пользователь может пойти. Важно сделать АРМ стабильно работающим и не вызывающим сложности даже у низкоквалифицированных сотрудников. АРМы у компании «Архио» очень удобные. Сотрудники работают только сканером штрихкода, при этом сверяют с экраном размеры по чертежу, который находится на Google Drive. Эти АРМы показывают стабильность своей работы и не вызывают никаких ошибок».
На нашем складе готовой продукции хранятся заказы до момента отгрузки. Раньше при комплектации каждого заказа сотрудники вручную писали на бумажке, изделия с какими артикулами лежат на конкретной палете. К каждой приклеивалась своя бумага с информацией. В процессе отгрузки в накладную вручную вбивалась информация со всех бумаг. Для крупных заказов накладные могли собираться в течение нескольких часов.
Сейчас на этапе комплектации заказа в системе учёта «1С:УНФ» появляется информация о том, на какой паллете какие изделии лежат. Для формирования накладных считываются штрих-коды с каждой палеты: необходимые для отгрузки документы формируются автоматически. Весь процесс занимает несколько минут. Исключены ошибки при отгрузке, так как никто и ничего не вводит руками. Человеческий фактор сведён к нулю.
Как уже было сказано, монтажникам приходилось вручную перебирать изделия с разных палет, чтобы найти все изделия для одного комплекта. Сейчас они получают палеты, на которых наша продукция разложена для отдельного комплекта.
На каждое изделие приклеена наклейка с QR-кодом. Прочитав её с помощью смартфона, монтажник попадает на наш сайт, где видит следующую информацию:
-
номер заказа;
-
артикул изделия и его чертёж;
-
чертёж комплекта, в котором используется данная продукция, и чертёж фасада в целом.
Теперь вся информация, необходимая для монтажа, хранится в одном месте. Рабочие сразу понимают, куда и как должны монтироваться изделия с каждой палеты. Им не нужно перебирать отгруженную продукцию, использовать бумажные чертежи или инструкции при сборе комплекта из разрозненных элементов. Процесс монтажа стал проще. Мы сотрудничаем с крупными застройщиками, и они говорят, что такая удобная комплектация заказов пока есть только у нас.
-
Ускорили процесс проверки качества изделий в три раза.
-
Исключили ошибки при комплектации заказов.
-
Сократили процесс оформления накладных с нескольких часов до нескольких минут.
-
Но самое главное – упростили процесс монтажа наших изделий непосредственно на строительных объектах.
Мы планируем автоматизировать и другие участки производства: в частности, учёт сырья и материалов. Это позволит нам лучше планировать закупки. Чтобы понимать, какой мастер какое изделие сделал, хотим ввести автоматизированный учёт трудозатрат. Это цели на ближайшие месяцы.
Чтобы не пропустить интересную для вас статью о малом бизнесе, подпишитесь на наш Telegram-канал, страницу в «ВКонтакте» и канал на «Яндекс.Дзен».