Toyota - одна из самых преуспевающих компаний мира. А её концепцию бережливого производства и целостный подход к организации бизнеса изучают в самых престижных бизнес-школах мира. Дао Toyota состоит из двух основных компонентов - непрерывного совершенствования и уважения к людям. Эта книга не только поможет понять, что позволило Toyota достичь выдающихся успехов, здесь вы также найдете множество идей, которые помогут вам выработать свой собственный подход к бизнесу и создать свою систему, своё дао в любой организации. С разрешения компании SmartReading мы публикуем саммари - «сжатую» версию - бестселлера Джеффри Лайкера «Дао Toyota».
SmartReading – проект сооснователя одного из ведущих российских издательств деловой литературы «Манн, Иванов и Фербер» Михаила Иванова и его партнёров. SmartReading выпускает так называемые саммари – тексты, в сжатой форме излагающие ключевые идеи бестселлеров жанра нон-фикшн. Таким образом, люди, которые по каким-то причинам не могут оперативно прочесть полные версии книг, могут познакомиться с их главными идеями и тезисами. SmartReading использует в своей работе подписную бизнес-модель.
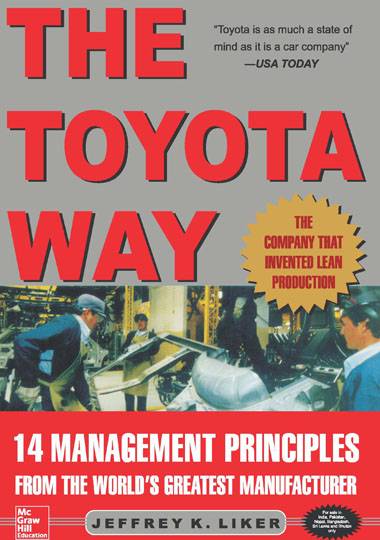
и бережливое производство
Самым выдающимся достижением Toyota является её производственная философия, которую называют производственной системой Toyota - TPS. TPS - следующая ступень в развитии эффективного бизнеса после системы массового производства, которую изобрёл Генри Форд. За пределами Toyota TPS часто называют бережливым производством - lean production. Бережливое производство - это процесс, который включает пять этапов:
- Определение ценности для потребителя;
- Выстраивание последовательного потока создания этой ценности;
- Обеспечение непрерывности этого потока;
- Обеспечение «вытягивания» от заказчика;
- Стремление к совершенству.
Принципы, на которых строится философия TPS:
-
Зачастую лучше остановить станок и прекратить производить детали. Это нужно для того, чтобы избежать перепроизводства - основного вида потерь в TPS.
-
Зачастую лучше создать некоторый запас готовых изделий, чтобы график производства был более сбалансированным, вместо того чтобы производить продукцию в соответствии с текущими колебаниями потребительского спроса.
-
Далеко не всегда нужно, чтобы рабочие изготавливали детали как можно быстрее. Скорость изготовления деталей определяется требованиями потребителя.
-
К использованию информационных технологий и автоматизации следует подходить избирательно, предпочитая им в ряде случаев ручную работу, даже если кажется, что автоматизация окупится, позволяя сократить количество рабочих.
Часто компании ошибочно полагают, что набор инструментов бережливого производства и философия бережливого производства - это одно и то же. Философия бережливого производства, в основе которой лежит дао Toyota, предполагает очень глубокую и всестороннюю культурную трансформацию.
США знакомы с TPS не менее двух десятилетий (в Toyota эта система в том или ином виде действует более 40 лет.) Но американские компании берут на вооружение только отдельные инструменты бережливого производства, не понимая, как работает система в целом. Обычно менеджмент использует несколько таких технических инструментов и, стараясь подойти к делу профессионально, создаёт техническую же систему. Но они не понимают, что на самом деле в основе TPS лежит нечто совсем иное: непрерывное совершенствование. В модели, которая включает четыре группы принципов, большинство компаний способны лишь «барахтаться» на уровне «процесса».
устранение потерь
Производственная система Toyota и дао Toyota - не одно и то же. TPS представляет собой нетрадиционный подход к управлению и работе, который требует сокращения неэффективных затрат при одновременном улучшении условий труда сотрудников и качества обслуживания для потребителей. А дао Toyota представляет собой фундамент для производственной культуры Toyota, что обеспечивает эффективную работу всей системы в целом. Хотя данный подход родился на автомобилестроительном предприятии, его в последние десятилетия успешно применяют в других отраслях бизнеса, в том числе и в сфере услуг.
Применяя TPS, в первую очередь следует оценить производственный процесс с точки зрения потребителя. Первый вопрос в TPS всегда один: «Чего ждёт от этого процесса потребитель?» (Речь идёт как о внутреннем потребителе, который работает с изделием на последующих операциях производственной линии, так и о конечном, внешнем потребителе.) Так определяется ценность. Посмотрев на процесс глазами потребителя, вы поймёте, на каких стадиях добавляется ценность, а на каких - нет. Это применимо к любому процессу: производству, обмену информацией или обслуживанию.
Рассмотрим пример ручной сборки шасси грузовика на сборочной линии.
Оператор производит много действий, но лишь немногие из них добавляют изделию ценность, которая важна для потребителя. В данном случае выявлено лишь три операции, которые добавляют ценность. Ряд других операций также необходим, хотя они не создают ценности. Например, оператор должен протянуть руку, чтобы взять инструмент. Задача состоит в том, чтобы на операции, которые не добавляют изделию ценность, затрачивалось как можно меньше времени. Для этого инструменты и детали должны подаваться как можно ближе к месту сборки.
Toyota выявила семь основных видов потерь - действий или затрат, не добавляющих ценности при осуществлении производственных и бизнес-процессов. Эти потери возможны не только на производственной линии, но и при разработке продукта, принятии заказов и в делопроизводстве. Существует и восьмой вид потерь, который был добавлен к списку автором книги.
- Перепроизводство.
- Ожидание (потери времени).
- Лишняя транспортировка или перемещение.
- Излишняя обработка (в том числе и из-за брака).
- Избыток запасов.
- Лишние движения.
- Брак.
- Нереализованный творческий потенциал сотрудников.
и подход с точки зрения бережливого производства
При традиционном подходе к совершенствованию процесса учитывается прежде всего локальная эффективность - «посмотри на оборудование, на операции, добавляющие ценность, и сделай период безотказной работы длиннее, рабочий цикл короче, а где можно - замени человека автоматом». В результате эффективность отдельной операции возрастает, но это не оказывает ощутимого влияния на поток создания ценности в целом.
Если перестраивать производство с точки зрения бережливого мышления, основной потенциал совершенствования - устранение огромного числа операций, где не создаётся добавленная ценность. При этом время, которое затрачивается на создание добавленной ценности, также сокращается.
В бережливом производстве рабочие места организованы и действуют в соответствии с последовательностью технологических операций. Это необходимо для обеспечения потока единичных изделий (услуг), которые одно за другим проходят различные технологические операции, например, сварку, сборку, упаковку. Скорость такой обработки определяется нуждами потребителя, которого нельзя заставлять ждать.
14 основных принципов сгруппированы в четыре категории:
- Философия долгосрочной перспективы;
- Правильный процесс даёт правильные результаты (речь идёт об использовании ряда инструментов TPS);
- Добавляй ценность организации, развивая своих сотрудников и партнёров;
- Постоянное решение фундаментальных проблем стимулирует непрерывное обучение.
Принцип 1. Принимайте управленческие решения с учётом долгосрочной перспективы, даже если это наносит ущерб краткосрочным финансовым целям.
• Используйте системный и стратегический подходы при постановке целей, причем все оперативные решения должны быть подчинены такому подходу. Каждый руководитель должен осознать своё место в истории компании и стараться вывести её на более высокий уровень. Работайте над организацией, совершенствуйте и перестраивайте её, двигаясь к главной цели, которая важнее, чем получение прибыли. Концептуальное понимание своего предназначения - фундамент всех остальных принципов.
• Основная задача организации - создавать ценность для потребителя, общества и экономики. Оценивая любой вид деятельности в компании, учитывайте, решает ли она эту задачу.
• Будьте ответственными. Стремитесь управлять своей судьбой. Верьте в свои силы и способности. Отвечайте за то, что делаете, поддерживайте и совершенствуйте навыки, которые позволяют вам производить добавленную ценность.
даёт правильные результаты
Принцип 2. Процесс в виде непрерывного потока способствует выявлению проблем.
• Перестройте технологический процесс так, чтобы создать непрерывный поток, эффективно обеспечивающий добавление ценности. Сократите до минимума время на простой незавершенной работы.
• Создавайте поток движения изделий или информации и налаживайте связи между процессами и людьми, чтобы любая проблема выявлялась немедленно.
• Этот поток должен стать частью организационной культуры, понятной для всех. Это ключ к непрерывному совершенствованию и развитию людей.
Принцип 3. Используйте систему вытягивания, чтобы избежать перепроизводства.
• Сделайте так, чтобы внутренний потребитель, который принимает вашу работу, получил то, что ему требуется, в нужное время и в нужном количестве. Основной принцип: при системе «точно вовремя» запас изделий должен пополняться только по мере их потребления.
• Сведите к минимуму незавершённое производство и складские запасы. Держите в запасе небольшое число изделий и пополняйте их по мере того, как их забирает потребитель.
• Будьте восприимчивы к ежедневным колебаниям потребительского спроса, которые дают больше информации, чем компьютерные системы и графики. Это поможет избежать потерь при скоплении лишних запасов.
Понять эту концепцию проще всего на примерах из повседневной жизни. Вы регулярно заправляете машину бензином. Заполняете ли вы бак по графику? Не приходило ли вам в голову заполнять его раз в неделю по понедельникам? Сомневаюсь. Заполняя его в таком режиме, вы бы быстро обнаружили, что иногда утром в понедельник в этом нет никакой необходимости, а порой бензин заканчивается задолго до наступления понедельника. По всей вероятности, вы заедете на бензоколонку, когда увидите, что бензин в баке заканчивается.
Принцип 4. Распределяйте объём работ равномерно (хейдзунка): «работайте как черепаха, а не как заяц».
• Устранение потерь - лишь одно из трёх условий успеха бережливого производства. Устранение перегрузки людей и оборудования и сглаживание неравномерности графика производства не менее важны.
• Работайте над равномерным распределением нагрузки во всех процессах, связанных с производством и обслуживанием. Такова альтернатива чередованию авралов и простоев, характерных для массового производства.
Хейдзунка представляет собой выравнивание производства как по объёму, так и по номенклатуре изделий. Чтобы предотвратить резкие взлёты и падения, продукция выпускается не в порядке поступления заказов потребителя. Сначала в течение некоторого периода собираются заказы, после чего их выполнение планируется таким образом, чтобы каждый день производить одинаковый ассортимент продукции в одинаковом количестве.
Принцип 5. Сделайте остановку производства с целью решения проблем частью производственной культуры, если того требует качество.
• Качество определяет для потребителя ценность вашего предложения. Используйте все доступные современные методы обеспечения качества.
• Создавайте оборудование, которое способно самостоятельно распознавать проблемы и останавливаться при их выявлении. Разработайте визуальную систему извещения лидера команды и её членов о том, что машина или процесс требуют их внимания. Дзидока (машины с элементами человеческого интеллекта) - фундамент для «встраивания» качества.
• Позаботьтесь о том, чтобы в организации существовала система поддержки, готовая к оперативному решению проблем и осуществлению корректирующих действий.
• Принцип остановки или замедления процесса должен обеспечивать получение необходимого качества «с первого раза» и стать неотъемлемой частью производственной культуры компании. Это повысит производительность в перспективе.
При бережливом производстве критически важно сразу производить качественные изделия. Поскольку уровень запасов очень низкий, при проблемах с качеством вы не можете рассчитывать на буферный запас
Принцип 6. Стандартные задачи - основа непрерывного совершенствования и делегирования полномочий сотрудникам.
• Используйте стабильные, воспроизводимые методы работы, это позволит сделать результат более предсказуемым, повысит слаженность работы, а выход продукции будет более равномерным. Это основа потока и вытягивания.
• Фиксируйте накопленные знания о процессе, стандартизируя лучшие на данный момент методы. Не препятствуйте творческому самовыражению работников, направленному на повышение стандарта; закрепляйте достигнутое новым стандартом. Тогда опыт, накопленный одним сотрудником, можно передать тому, кто придёт ему на смену.
Принцип 7. Используйте визуальный контроль, чтобы ни одна проблема не осталась незамеченной.
• Используйте простые визуальные средства, чтобы помочь сотрудникам быстро определить, где они соблюдают стандарт, а где отклонились от него.
• Не стоит использовать компьютерный монитор, если он отвлекает рабочего от рабочей зоны.
• Создавайте простые системы визуального контроля на рабочих местах, способствующие поддержанию потока и вытягивания.
• По возможности, сократите объём отчетов до одного листа, даже если речь идёт о важнейших финансовых показателях.
В Японии ведётся работа по программе «5S», которая включает ряд мероприятий по устранению потерь, порождающих ошибки, дефекты и травмы на рабочем месте (по-японски они называются сейри, сейтон, сейсо, сейкецу и сицуке, по-английски - sort, stabilize, shine, standardize, sustain).
- Сортируй (убери ненужное) - рассортируй предметы или информацию и оставь лишь то, что нужно, избавившись от ненужного.
- Соблюдай порядок (упорядочи) - «У всего свое место, и всё на своих местах».
- Содержи в чистоте - процесс уборки часто является формой проверки, которая позволяет выявить отклонения и факторы, которые могут вызвать аварию и нанести ущерб качеству или оборудованию.
- Стандартизируй - разрабатывай системы и процедуры для поддержания и отслеживания первых трех S.
- Совершенствуй - постоянно поддерживай рабочее место в порядке, реализуй непрерывный процесс совершенствования.
Визуальный контроль включает любые средства коммуникации, используемые на производстве, которые позволяют с первого взгляда понять, как должна выполняться работа и есть ли отклонения от стандарта.
Принцип 8. Используйте только надёжную, испытанную технологию.
• Технологии призваны помогать людям, а не заменять их. Часто стоит сначала выполнять процесс вручную, прежде чем вводить дополнительное оборудование.
• Новые технологии часто ненадёжны и с трудом поддаются стандартизации, а это ставит под угрозу поток. Вместо непроверенной технологии лучше использовать известный, отработанный процесс.
• Прежде чем вводить новую технологию и оборудование, следует провести испытания в реальных условиях.
• Откажитесь от технологии, которая идёт вразрез с вашей культурой, может нарушить стабильность, надёжность или предсказуемость.
• И всё же поощряйте своих людей не забывать о новых технологиях, если речь идёт о поисках новых путей. Оперативно внедряйте зарекомендовавшие себя технологии, которые прошли испытания и делают поток более совершенным.
развивая своих сотрудников и партнёров
Принцип 9. Воспитывайте лидеров, которые досконально знают своё дело, исповедуют философию компании и могут научить этому других.
• Лучше воспитывать своих лидеров, чем покупать их за пределами компании.
• Лидер должен не только выполнять поставленные перед ним задачи и иметь навыки общения с людьми. Он должен исповедовать философию компании и подавать личный пример отношения к делу.
• Хороший лидер должен знать повседневную работу как свои пять пальцев, лишь тогда он сможет стать настоящим учителем философии компании.
В Toyota принято говорить: «Прежде чем создавать машины, мы создаём людей». Цель лидера Toyota - развивать людей, чтобы они могли внести достойный вклад в общее дело, умели думать и следовали принципам дао Toyota на всех уровнях организационной структуры.
Принцип 10. Воспитывайте незаурядных людей и формируйте команды, исповедующие философию компании.
• Создавайте сильную, стабильную производственную культуру с долговечными ценностными ориентациями и убеждениями, которые разделяют и принимают все в компании.
• Обучайте незаурядных людей и рабочие команды действовать в соответствии с корпоративной философией, которая позволяет достичь исключительных результатов. Трудитесь не покладая рук над укреплением производственной культуры.
• Формируйте межфункциональные группы, чтобы повысить качество и производительность и усовершенствовать поток за счёт решения сложных технических проблем. Вооружите людей инструментами, которые позволяют совершенствовать компанию.
• Неустанно обучайте людей работать в команде на общую цель. Освоить работу в команде должен каждый.
Принцип 11. Уважайте своих партнёров и поставщиков, ставьте перед ними трудные задачи и помогайте им совершенствоваться.
• Уважайте своих партнёров и поставщиков, относитесь к ним как к равноправным участникам общего дела.
• Создавайте для партнеров условия, стимулирующие их рост и развитие. Тогда они поймут, что их ценят. Ставьте перед ними сложные задачи и помогайте решать их.
фундаментальных проблем
стимулирует непрерывное обучение
Принцип 12. Чтобы разобраться в ситуации, надо увидеть всё своими глазами (генти генбуцу).
• Решая проблемы и совершенствуя процессы, вы должны увидеть происходящее своими глазами и лично проверить данные, а не теоретизировать, слушая других людей или глядя на монитор компьютера.
• В основе ваших размышлений и рассуждений должны лежать данные, которые проверили вы сами.
• Даже представители высшего руководства компании и руководители подразделений должны увидеть проблему своими глазами, лишь тогда понимание ситуации будет подлинным, а не поверхностным.
Принцип 13. Принимайте решение не торопясь, взвесив все возможные варианты; внедряя его, не медлите (немаваси).
• Не принимайте однозначного решения о способе действий, пока не взвесите все альтернативы. Когда вы решили, куда идти, следуйте избранным путём без промедления, но соблюдайте осторожность.
• Немаваси - это процесс совместного обсуждения проблем и потенциальных решений, в котором участвуют все. Его задача - собрать все идеи и выработать единое мнение, куда двигаться дальше. Хотя такой процесс и занимает довольно много времени, он помогает осуществить более масштабный поиск решений и подготовить условия для оперативной реализации принятого решения.
Если процесс принятия решения был правильным, руководство может простить, что принятое решение не дало ожидаемых результатов. Если же решение случайно оказалось удачным, но было принято поспешно, вероятность получить выговор босса куда более велика.
Рассмотрение вопроса при принятии решения включает пять основных составляющих:
-
Выяснить, что происходит в действительности, включая генти генбуцу.
-
Понять первопричины внешних проявлений происходящего - пять раз задать вопрос «Почему?».
-
Рассмотреть все альтернативные решения и детально обосновать выбор решения, которому оказано предпочтение.
-
Добиться единодушия членов команды, включая сотрудников Toyota и внешних партнёров.
-
Использовать при осуществлении четырех перечисленных шагов самые эффективные средства коммуникации, желательно излагать всю информацию на одной странице.
Принцип 14. Станьте обучающейся структурой за счет неустанного самоанализа (хансей) и непрерывного совершенствования (кайдзен).
• Как только процесс стабилизировался, используйте инструменты непрерывного совершенствования, чтобы выявить первопричины неэффективной работы, и принимайте действенные меры.
• Создайте такой процесс, который почти не требует запасов. Это позволит выявить потери времени и ресурсов. Когда потери очевидны для всех, их можно устранить в ходе непрерывного совершенствования (кайдзен).
• Оберегайте базу знаний об организации своей компании, не допускайте текучести кадров, следите за постепенным продвижением сотрудников по службе и сохранением накопленного опыта.
• При завершении основных этапов и окончании всей работы произведите анализ (хансей) её недостатков и открыто говорите о них. Разработайте меры, которые предупредят повторение ошибок.
• Вместо того чтобы изобретать колесо, когда начинаете новую работу или когда появляется новый сотрудник, научитесь стандартизовать лучшие приёмы и методы.
Один из самых ярких примеров дао Toyota в действии - разработка автомобиля Prius. Его создание стало настоящим переворотом в истории фирмы и во многом изменило Toyota как компанию.
Обстановка начала 1990-х годов вызывала у руководителей Toyota определённые опасения. Проблема заключалась в том, что всё складывалось слишком хорошо. Японская экономика находилась на подъёме. Успехи Toyota были просто сенсационными. Многие компании в таких условиях считают, что могут почивать на лаврах. Но, по мнению лидеров Toyota, компанию, которая не понимает, что наступил кризис, и не чувствует насущной потребности постоянно совершенствовать методы работы, ждёт катастрофа.
В то время в Toyota существовала отлаженная система разработки модификаций существующих моделей автомобилей, но система разработки в целом не менялась несколько десятков лет. Toyota никогда не забывает о возможности кризиса, и порой лидеры компании провоцируют кризисную ситуацию умышленно, если это может пойти на пользу делу.
Было намечено создать компактный, экономичный и одновременно просторный автомобиль. Поначалу проект не предполагал создания автомобиля гибридного типа. Были поставлены две цели:
- создать новый подход к производству автомобиля XXI века;
- создать новый подход к разработке автомобиля XXI века.
К будущему автомобилю предъявлялись следующие требования:
- Вместительный салон за счёт максимальной длины колёсной базы.
- Относительно высокое размещение сиденья, чтобы было удобно садиться в машину и выходить из неё.
- Обтекаемая форма, высота 1500 мм, чуть ниже, чем у мини-вэна.
- Низкий расход топлива - 20 км на литр (47,5 мили на галлон).
- Компактный, горизонтально размещенный двигатель с бесступенчатой автоматической коробкой передач (что способствует более эффективному использованию топлива).
Первая стадия проекта иллюстрирует применение трёх принципов дао Toyota.
Принцип 9. Менеджеры высшего уровня активно поддерживали этот совершенно абстрактный проект, который был делом отдалённого будущего, но который во многом определял это будущее, не жалея времени на еженедельные встречи с рабочей группой.
Принцип 10. За сложнейший проект, который был жизненно важным для компании, взялись лучшие специалисты. Не жалея сил, они работали сверхурочно, чтобы уложиться в самые сжатые сроки.
Принцип 12. Рабочая группа решила, что презентации абстрактных идей недостаточно, поскольку они слишком далеки от создания реальной машины. Члены группы разработали чертёж в масштабе 1:2, чтобы высшее руководство компании могло получить представление о будущем автомобиле.
В начале работы над проектом основное внимание уделялось разработке концепции и исследованию альтернативных технологий. С 1995 года программа имела чёткую направленность на производство первого серийного гибридного автомобиля.
Поскольку речь шла о новой технологии производства и о создании новой производственной системы, план был рассчитан на три года. За первый год предполагалось изготовить опытный образец. Следующий год планировалось отвести на исследования и проработку деталей, с тем чтобы на третий год направить основные усилия на доработку серийного варианта и подготовку производства.
Критики Toyota говорят о нецелесообразности огромных капиталовложений в проект Prius, которые, по приблизительным оценкам, составляют от сотен миллионов до миллиарда долларов, и выражают сомнения в окупаемости инвестиций. Чтобы окупить свои капиталовложения, Toyota должна продавать 300 тысяч гибридных автомобилей в год. Пока Toyota не вышла на этот уровень.
Но цели создания Prius шли дальше немедленного повышения доходности компании. Человечество получило первую серийно выпускаемую машину, которая наносит значительно меньший ущерб окружающей среде.
-
Разработка этого автомобиля позволила Toyota воспитать плеяду молодых инженеров, которые теперь умеют создавать новую технологию.
-
Создание гибридных двигателей в ходе работ по проекту Prius позволило Toyota развернуть новые производственные мощности, и теперь она продаёт комплектующие другим производителям.
-
И, наконец, это привело к коренному изменению методов разработки автомобилей, которые сейчас используются при проектировании всех новых моделей.
С учётом всего этого создание Prius окупилось сторицей. Сотрудники Toyota сделали всё, чтобы своими силами добиться поставленной цели, и при этом обрели опыт, знания и новые возможности.
Применение производственной системы Toyota за пределами производственных цехов вполне возможно, но требует творческого подхода. Разумеется, основные принципы TPS применимы и к процессам управления.
В организациях, занимающихся административными вопросами или работающих в сфере оказания услуг, люди сидят за столом, работают на компьютере, обсуждают различные вопросы, проводят совещания и обычно заняты разными делами. Выявить поток в их работе далеко не так просто, как проследить физическое перемещение изделия по мере его преобразования на производстве.
Создание потока в таких организациях включает пять этапов:
- Определить потребителя процессов и добавленную ценность, которую потребитель ожидает получить.
- Отделить повторяющиеся процессы от уникальных в своём роде процессов и изучить вопрос о том, как можно применить TPS к повторяющимся процессам.
- Составить карту потока с указанием добавляющих и не добавляющих ценность операций.
- Творчески осмыслить применение принципов подхода Toyota к данным процессам, составив карту усовершенствованного потока создания ценности, который предполагается получить.
- Приступить к реализации плана и учиться на собственном опыте, применяя принципы цикла PDCA и стараясь постепенно включить в его сферу менее часто повторяющиеся процессы.
Рассмотрим эти процессы на примере Canada Post Corporation (CPC) - почтовой службы Канады. В её структуре на 22 основных сортировочных предприятиях работают около 57 тысяч сотрудников. Клиенты обслуживаются в 900 тысячах пунктах в Канаде. Доставка осуществляется по 13 млн. адресов внутри страны. В середине 1990-х годов CPC начала применять методы бережливого производства к операциям сортировки и доставки корреспонденции.
До начала работ по применению принципов бережливого производства в 1995 году ситуация была сложной. Предприятия, занимавшиеся сортировкой, представляли собой настоящие склады. Первоочередное внимание там уделялось автоматизации, которая позволяла ускорить работу сортировочного оборудования. При этом большая часть потерь между операциями сортировки, добавляющими ценность, игнорировалась. Процесс преобразования CPC в бережливое предприятие проходил в три этапа:
- «Точечный кайдзен» - попытки усовершенствовать отдельные составляющие потока создания ценности;
- Выработка полномасштабного представления о потоке создания ценности с системным анализом потока и его изменением;
- Создание бережливого предприятия.
«Сортировка почтовой корреспонденции и посылок занимает секунды, транспортировка - минуты, хранение - часы, а доставка - дни. Наше предприятие оказалось попросту складом»
Кроме того, им удалось добиться и других результатов:
- на 28% снизилось время транспортировки корреспонденции;
- на 37% уменьшилось время выполнения заказа;
- на 27% сократилось промежуточное складирование.
в бережливое обучающееся предприятие
Самый сложный и в то же время основной вопрос для компаний, которые хотят учиться у Toyota: как создать организацию, ориентирующую и объединяющую людей, каждый из которых несет в себе её генетический код, а все вместе - постоянно учатся создавать добавленную ценность для потребителя?
-
Начинайте с воздействия на техническую систему; сразу после этого беритесь за изменение производственной культуры.
-
Обучайтесь прежде всего на практике и лишь потом - занимайтесь теорией.
-
Используйте схематичное представление потока материала и информации для разработки будущих концепций, которая научит вас видеть.
-
Перестройте организационную структуру в соответствии с потоком добавления ценности.
-
Относитесь к этой работе как к обязательной. Если компания рассматривает создание бережливого предприятия как нечто интересное, но не обязательное, чем можно заниматься в свободное время или когда заблагорассудится, она ничего не добьётся.
-
Переходите на бережливое производство, не дожидаясь кризиса.
-
Приведите систему показателей в соответствие с принципами потока создания ценности. «Вы получаете то, что измеряете».
-
Опирайтесь на историю своей компании, чтобы найти собственный путь.
- Наймите или обучите лидеров в области бережливого производства и позаботьтесь о преемственности.
27 марта в Москве состоится семинар Джеффри Лайкера - автора бестселлера «ДАО TOYOTA» и лауреата 10 премий в области бережливого производства. Десятки российских компаний уже внедряют систему бережливого производства, но ни одна из них не достигла уровня Toyota. В чем же секрет? Ответ вы узнаете на семинаре. Билеты можно забронировать на сайте семинара, читателям Biz360 – специальная скидка 7% по промо-коду «biz360».
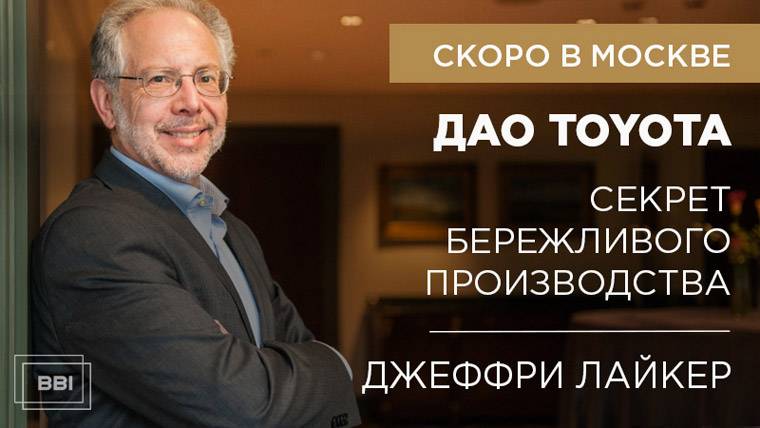
Саммари книги Карла Сьюэлла «Клиенты на всю жизнь»
Саммари книги Джима Коллинза «От хорошего к великому»
Саммари книги Марка Герзона «Лидерство через конфликт»